Rewiring Australia’s Approach: The Cable Recycling Innovation Sparked by Policy Failure
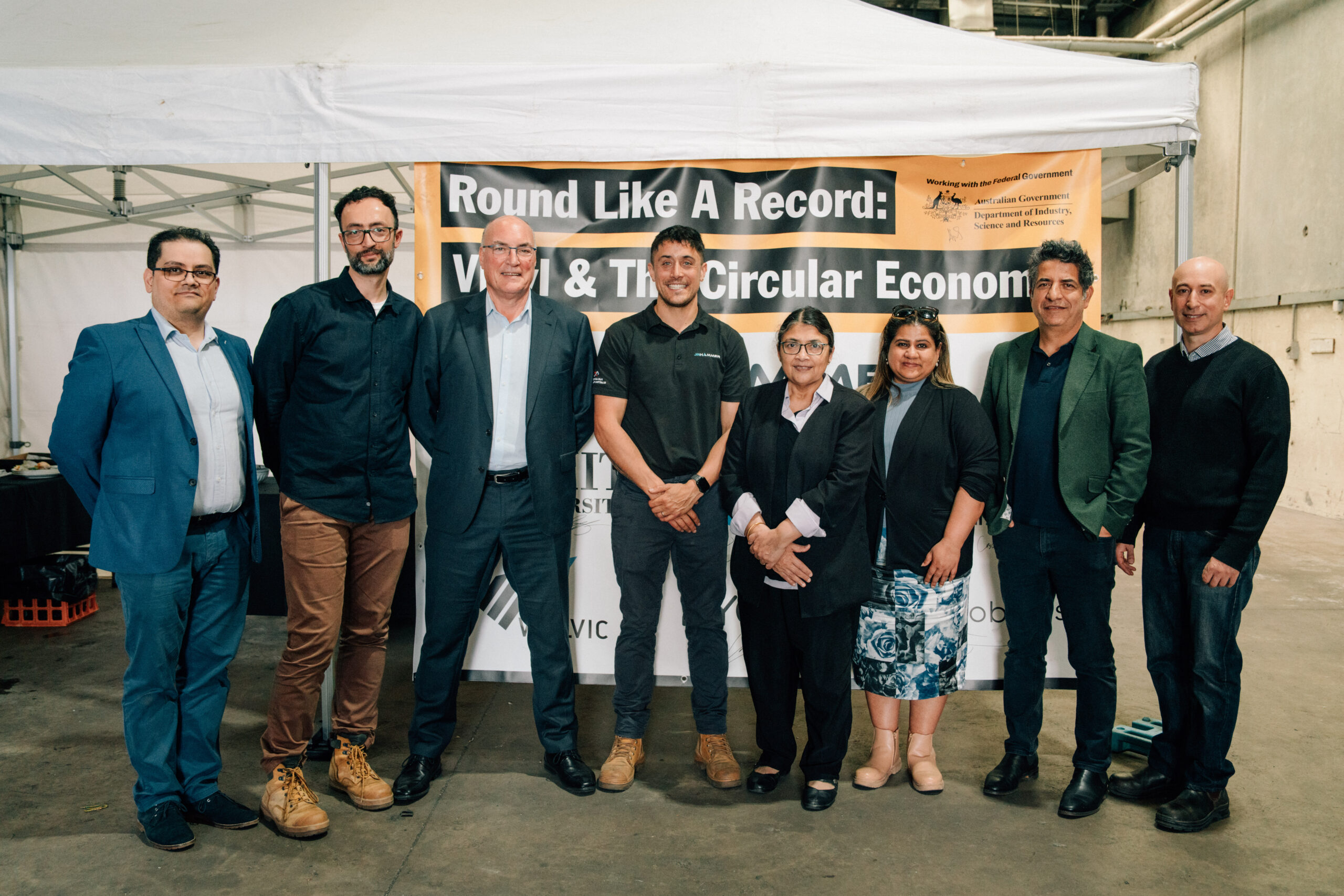
In 2018 Australia had a wake-up call came when China said no more to recycling exports, causing global disruption in waste management that exposed vulnerabilities that were ignored for decades.
The hidden crisis in cable waste management that emerged post-National Sword revealed how dependent the country had become on exporting waste problems rather than solving them.
Yet this policy failure catalysed cable waste recycling innovation, forcing Australian companies to develop advanced solutions that traditional methods couldn’t deliver, turning crisis into opportunity for those smart enough to embrace change.
The National Sword Shock: What Happened and Why It Mattered
China’s National Sword policy banned 24 types of recyclable materials in 2018, including plastics PE, PS, PVC, and PET, creating immediate global impact that caught Australia completely unprepared.
The statistics were staggering: before 2018, Australia exported over 4 million tonnes of waste annually, with 71% of recyclable materials sent to China. In 2016–17 alone, 1.25 million tonnes were shipped, including a significant 36% share of household kerbside plastics. Then came China’s National Sword policy, which triggered a 99% drop in global recyclable plastic imports.
Suddenly, all those established international waste trade flows were disrupted overnight, exposing just how fragile and unsustainable the system had become.
This policy shift went far beyond logistics as it exposed fundamental flaws in Australia’s waste management capabilities and forced a reckoning with its “export the problem” mentality, leaving the country’s recycling industry struggling to handle the redirected waste.
When China closed the door, Australia was forced to open its eyes to the urgent reality: develop local processing capabilities immediately or face mounting environmental and economic consequences.
The comfortable dependency that had defined Australia’s approach for decades vanished overnight, leaving us scrambling to address waste streams they’d never properly planned to handle domestically.
Australia’s Recycling Reality Check: Exposing Our Dependency and Infrastructure Gaps
The National Sword crisis exposed Australia’s limited recycling infrastructure locally, particularly the country’s inability to handle complex materials like cable waste.
The consequences were immediate and visible: stockpiles grew across the country, illegal dumping increased as disposal options disappeared, export bottlenecks created chaos, and growing public pressure demanded local solutions that were simply non-existent or too expensive to implement quickly.
The gaps became particularly apparent in processing mixed-material waste streams like cable waste. On a crisis scale, over 111 million tons of plastics will need new processing/disposal over the coming decade.
Traditional Australian recyclers had equipped themselves with only basic metal recovery capabilities by stripping copper and aluminium but lacked the technology and expertise for comprehensive material processing that could handle the full complexity of cable waste.
This outdated model left valuable resources trapped in materials destined for landfill, while the PVC components continued to accumulate as waste streams that nobody knew how to handle properly.
Why Electrical Waste Became a Critical Challenge
The cable waste problem perfectly illustrated the crisis: electrical cables contain valuable metals like copper and aluminium, but these are wrapped in problematic PVC components that present serious environmental and processing challenges.
When the National Sword policy hit, electrical contractors suddenly had severely limited recycling and disposal options for their cable waste, with mounting compliance pressures making proper disposal both urgent and expensive.
Only 3-5% of PVC is recycled in Australia annually, a critically low range that means the vast majority still ends up in landfill, a statistic that became impossible to ignore post-National Sword.
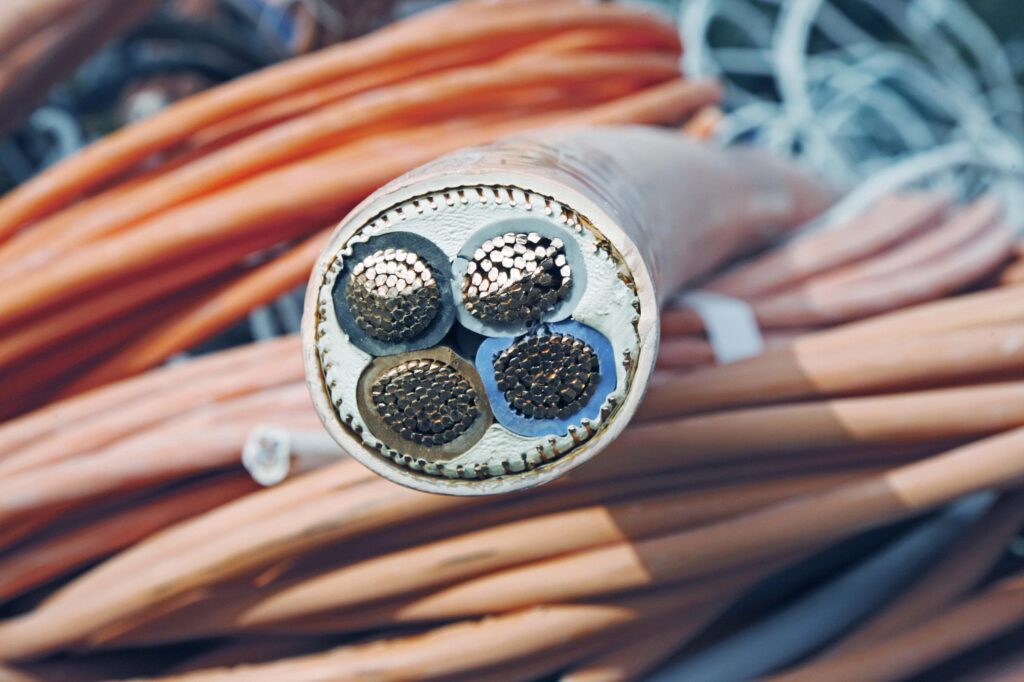
Traditional recyclers achieve around 50% recycling rates compared to what’s actually possible with advanced cable recycling technology, while the remainder adds to the world’s throwaway culture.
The growing ESG compliance requirements and environmental regulations transformed proper cable recycling from a nice-to-have into both an environmental necessity and a business imperative for electrical contractors who could no longer rely on the old dump-and-forget approach.
The Recycling Renaissance: How Policy Failure Sparked Technological Advancement
The National Sword crisis became Australia’s turning point for recycling, proving that policy failure can spark real and significant innovations.
When traditional approaches failed, innovators like JR Hammer stepped in with tailored solutions specifically designed for Australia’s new reality, proving that local innovation could solve distinctly local environmental challenges.
This period saw the emergence of research partnerships, government R&D support, and private investment in advanced recycling technology that transformed what was possible.
The breakthrough came through strategic partnerships with leading institutions: CSIRO, RMIT, and the Vinyl Council of Australia collaborated to develop cutting-edge technologies that could tackle previously unsolvable problems like comprehensive PVC recycling.
These partnerships represent a fundamental shift from basic material recovery to comprehensive circular economy solutions moving from the old mentality of strip-what-you-can, dump-the-rest to localised engineered systems that achieve exceptional recovery rates.
Cable waste became the new copper mine once JR Hammer developed the tools to extract maximum value from what others considered waste.
JR Hammer’s Solution: Advanced Machinery Meeting Australia’s New Reality
JR Hammer embodies Australia’s innovation response to the policy crisis, representing the smart, local technology solutions that achieved recycling independence through transparent, circular recycling solutions.
The company’s investment in European processing machinery and development of proprietary technologies delivers 90% recycling rates at 2.5 tons per hour capacity, dramatically outperforming the industry standard of 50% recovery at 400kg per hour.
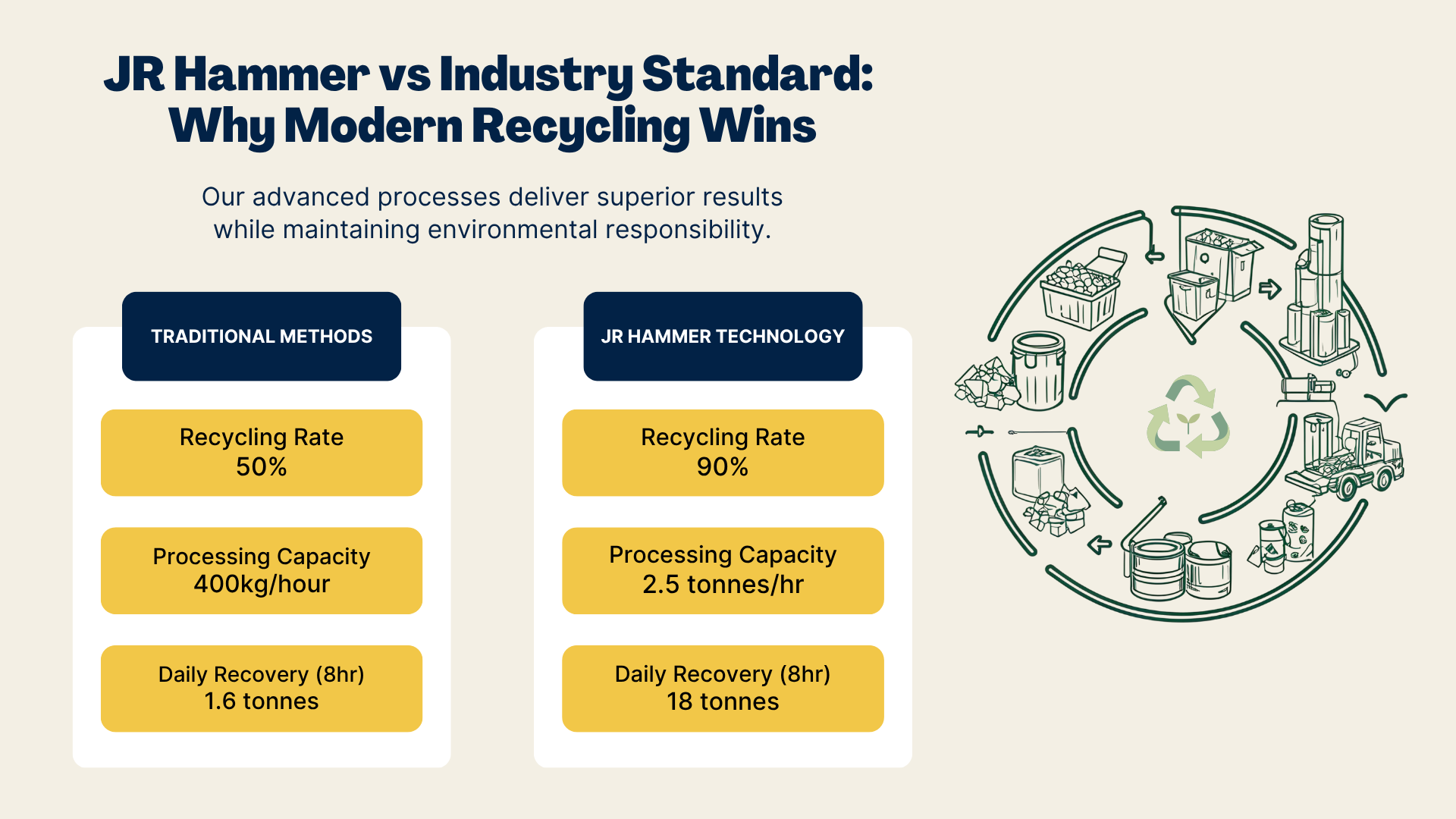
This approach focuses on prevention and reuse, highlights the economical ways to separate hard-to-recycle plastics, and represents genuine rethinking resource recovery where advanced recycling machinery transforms waste streams into valuable resources.
“We’re partnering with leading researchers and academics like CSIRO, RMIT, and the Vinyl Council of Australia to develop breakthrough technologies that can finally solve Australia’s PVC recycling challenge,” explains Josh, JR Hammer’s founder.
The company’s dedicated Melbourne facility demonstrates comprehensive material processing that recovers value from waste, proving that JR Hammer is truly powering sustainable change in Australia’s waste sector.
As upcoming environmental regulations make advanced recycling a necessity rather than a choice, early investment in the right recycling partners like JR Hammer who are engineered for tomorrow’s waste challenges help companies stay compliant and competitive in an increasingly demanding marketplace.
Turning Crisis into Competitive Advantage
The lessons from this policy-triggered crisis are undeniable: recycling isn’t broken, our systems were, but we can rebuild them better.
Smart, local technology like JR Hammer’s proves that achieving recycling independence is essential both economically and environmentally, while demonstrating that transparency in recycling processes has become a competitive differentiator in sustainable cable disposal.
The electrical industry’s waste challenge requires specialised, not generalised solutions, and blanket approaches simply can’t handle the complexity of modern industrial waste recycling solutions.
Today’s market leaders are companies that embraced change and invested in genuine circular economy solutions rather than clinging to outdated approaches that couldn’t deliver proper Australian recycling policy reform.
China may have closed the door on Australia’s recycling exports, but we opened a better one.
Experience the future of cable recycling with JR Hammer’s industry-leading technology to help you stay compliant, sustainable, and give your business the competitive edge it needs in a shifting regulatory and sustainability landscape.
Read more stories on our blog:
Rethinking waste: how JR Hammer is transforming cable recycling
Behind Recycling Certificates: What Actually Happens to Your Waste After Collection?